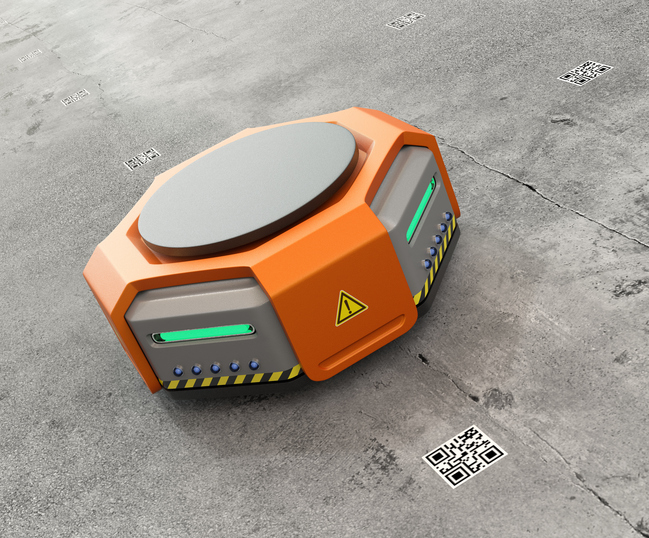
even today, most robots sold are of the “traditional” type: Permanently mounted, and requiring the installation of “safeguards” to keep people away from the robot’s hazardous zone (known as the “restricted space”). An automotive welding robot is a good example of this type of robot system. People are kept safe by being kept apart from the robot system.
Meanwhile, the safety considerations around mobile industrial equipment were addressed in standards such as the Industrial Truck Standards Development Foundation’s (ITSDF) B56.5 Safety Standard for Driverless, Automatic Guided Industrial Vehicles and Automated Functions of Manned Industrial Vehicles (the “AGV Safety Standard”).
The Problem with Today's Robot Standards
The proliferation of mobile, automated systems has complicated things. New technology has blurred the lines between R5.06- and B56.5-governed equipment, while also revealing the shortcomings of each set of safety standards.
What if you mount an industrial robot arm to an AGV? Or, what if the mobile unit has a greater degree of autonomy than a traditional AGV has? For these types of "mobile robots," which standard should take precedence and under which circumstances? The R5.06, the “Robot Safety Standard,” or the B56.5, the “AGV Safety Standard”?
The R15.08 Committee and the Future of Robot Safety Standards
An exploratory group compared the two existing standards and, in the summer of 2015, recommended that a new standard be developed to describe safety requirements for mobile robots and mobile robot systems.
The goal was to fill in gaps and resolve overlaps between the safety requirements described in the R15.06 and B56.5. The R15.08 committee was formed to carry this out.
Since then, the R15.08 committee has met several times to explore the boundaries and content of the two earlier standards (R15.06 and B56.5), agree on scope for the new work, develop an outline, and begin drafting content.
The R15.08 group met in San Jose, CA, on November 13 – 14, 2017. The goal of this meeting was to review and discuss a nearly complete first draft of Part 1 of the proposed R15.08 standard on Safety Requirements for Industrial Mobile Robots and Mobile Robot Systems.
Part 1 describes requirements for the Mobile Robot and as addressed to robot manufacturers. Work on Part 2 will begin next, describing safety requirements for a system of mobile robots, addressed to system integrators (installers).
Part 1 and Part 2 will be published together, with a target publication date of early 2019. Later, Part 3 will be drafted to provide guidance to users.