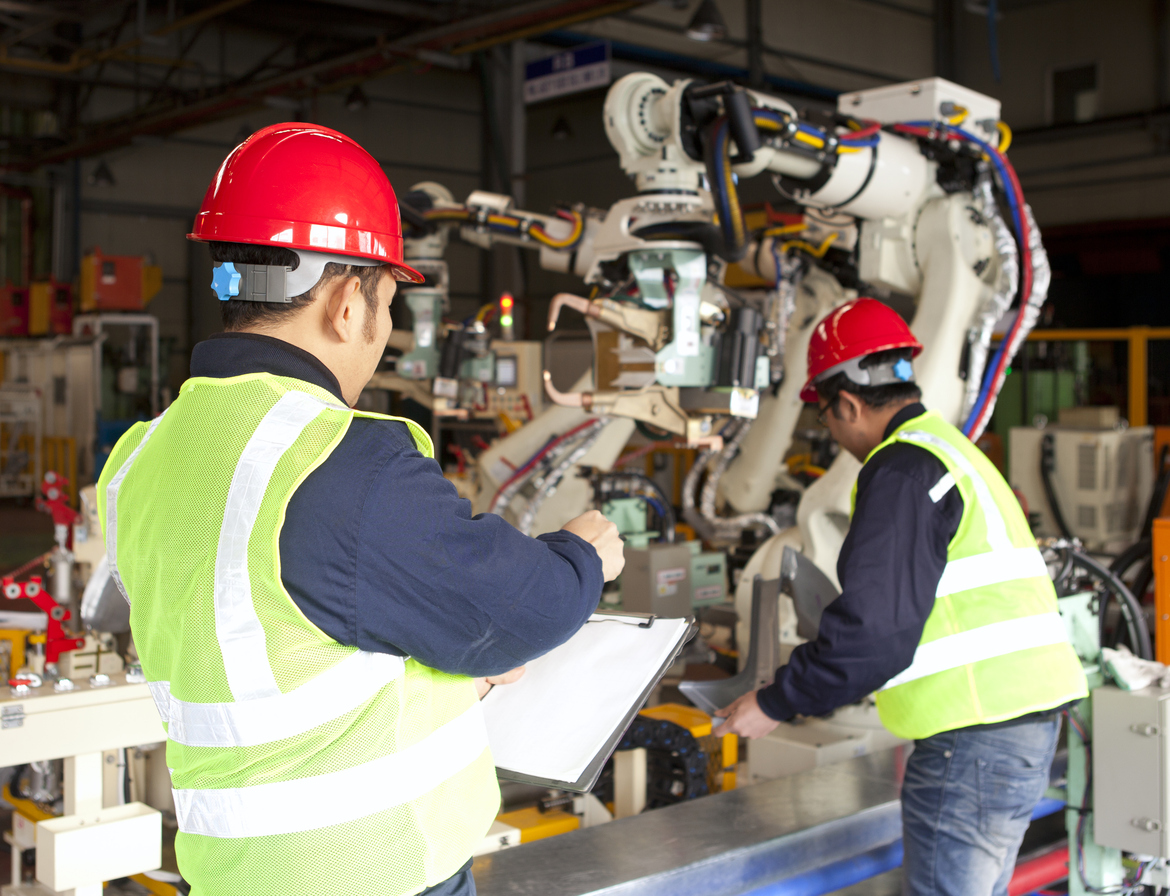
Overall robotics spend will climb to $13 billion in 2025. Much of this growth will be fueled by increasing demand in collaborative robots. As a portion of all robot sales, collaborative robots will grow from 3% in 2016 to 34% in 2025.
Collaborative robots are not suited to perform the heavy-duty tasks of industrial robots, however, they are smarter and feature advanced technology to perform more complex tasks, which is a major reason why they’re gaining popularity so quickly.
There are other reasons though, especially when you view the benefits of collaborative robots through the eyes of a manufacturing startup.
Collaborative Robots in Startups
Collaborative robots are particularly useful in most startup settings. They provide great opportunities for small companies to start competing with their larger competitors who have drastically higher production capabilities.
They do this several ways. Here are the major reasons collaborative robots are so popular amongst manufacturing startups:
- Low Initial Investment
Collaborative robots are far cheaper than industrial robots, but can provide similar productivity gains. Not only does this help startups justify the cost of automation, but it also helps these same startups realize quicker ROI once they do implement robotic solutions.
- Short Integration Period
Avoiding downtime is important for any manufacturer, and it’s no different for startups. A collaborative robotic solution can be implemented very quickly, sometimes in as little as 5 days. This keeps integration costs low – the cost of a robot and the cost of integration are two separate things.
- Easy to Use
Collaborative robots are notoriously easy to use. You don’t need highly trained programmers on the floor to use a collaborative robot – another way in which collaborative robots are cheaper – and they can be “taught” different skills quickly and easily.
For manufacturing startups, collaborative robots make sense more often than industrial robots do. The productivity they provide, along with their low costs, allow small companies to scale production quickly without a major upfront investment.
A great example of the role of collaborative robots in manufacturing startups is the partnership between Robotiq, a robotic systems integrator, and Lowercase, an eyewear startup located in the U.S. To learn more about collaborative robots and startups, read the case study here.