R
obotic machine tending is the automated process of tending a machine – typically a computer numerical control (CNC) machine. Usually this process is the loading of raw materials into the machine and unloading of finished parts out of the machine.
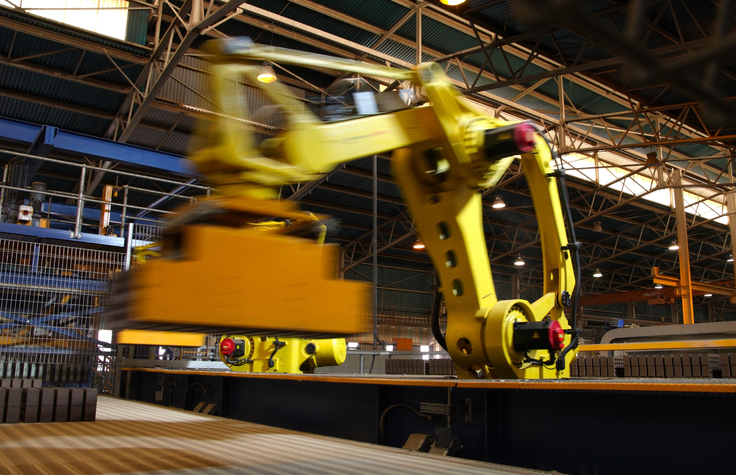
Robotic machine tending is differentiated from robotic material handling as the tending process involves more complexity. The robotic system often has to communicate with the CNC machine in one form or another, and has to perform a few different functions in a single application.
Common Applications for Robotic Machine Tending
Robotic machine tending is typically used for loading and unloading parts in the following applications:
- Grinding
- Milling and turning
- Injection molds
- Stamping, punching, trimming and forging
- Compression molds
- Welding
The specific processes a robotic system completes in each of these applications varies, but the common function is the loading and unloading of materials and parts.
Benefits of Robotic Machine Tending Systems
One of the main benefits of robotic machine tending is the drastically improved uptime when compared to manual loading and unloading. The only time the robot needs to stop is for regular maintenance, meaning the productivity of the machine being tended is not limited by manual labor. This gain in uptime leads to major productivity gains by boosting throughput.
On top of the increased uptime, robotic machine tending systems are more accurate and repeatable than manual loading and unloading. Not only can this increase the quality of parts produced, but it can reduce the amount of error in the machining process, maximizing throughput and minimizing wasted materials and time.
Robotic machine tending systems provide many benefits for manufacturers - chief among them are uptime and accurate repeatability. For anything from grinding to welding or milling and turning, robotic machine tending delivers productivity.
No comments:
Post a Comment